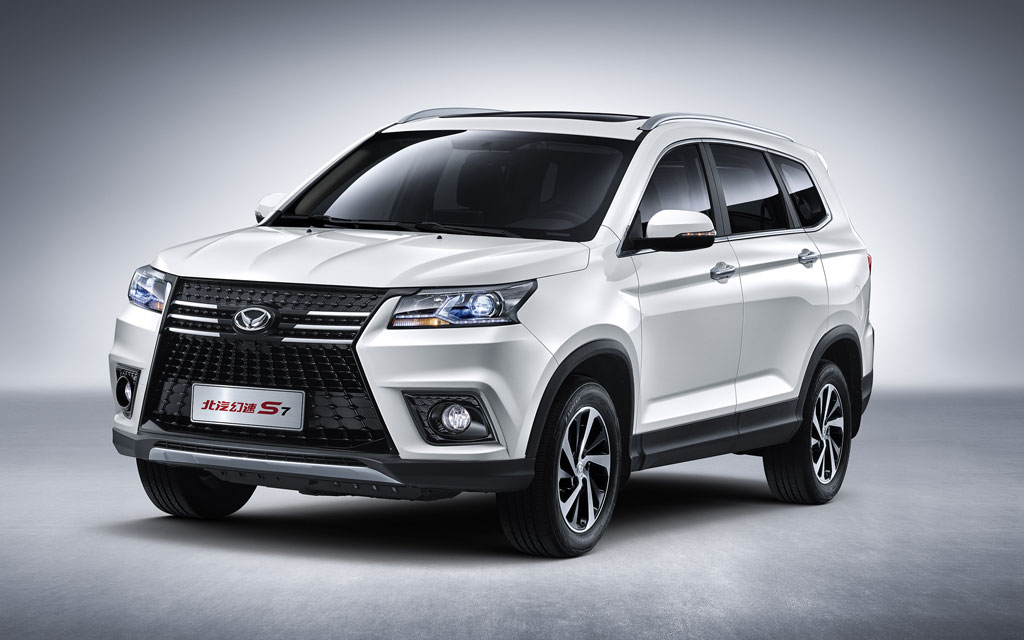
More and more local and international manufacturers are following KENBO’s footprint in China market by releasing various 7 seater SUV models and MPVs. Multiple investigator and reporters have visited and interviewed employees from KENBO factory at different level, finding their legend is not merely driven by market, but more importantly a responsibility for its employees and their own families.
During the launching period of revolutionary new SUV product S7, this responsibility will be further demonstrated by this legendary maker.
As the increase of passenger car sales increases in every market, more and more traffic accidents are seen and the figure of traffic death soars in the same curve with sales growth, leading to a market demand change from tool vehicle to a safety mobility space which KENBO has always upholds as its top responsibility from its birthday.
In the designing stage of the new S7, a series of strict crash test standards are set and a historically strong R&D team lead by the Chief Technical Officer of KENBO Headquarter is organized to work on the safety.
What did they do?
Target Setting
In the setting of general safety goal, KENBO sticks to its 3T (3 tiers) principle.
Tier 1 – Score in 50Km/h front impact on ridig wall, 64Km/h 40% bias impact、50Km/h side impact, Seat whiplash test.
Tier 2 – Score in dummy, including head, neck, chest and leg.
Tier 3 – Score in body deformation (B pillar acceleration, firewall intrusion, A pillar intrusion etc. ) and impact related parts (safety belt, airbag, steering column etc.).
Structure Design& Optimization
KENBO S7 is defined as a 5 star C-NCAP SUV following KENBO patented Cage Body design which is able to maximumly disperses and passes impacts to each beam to reduce to passenger within the cage.
Based on S7 front layout and loading path, in consideration of the requirements of front impact and bias impact, the weakest point on the body was detected through 4 rounds (hundreds times of tests) CAE simulation and have been redesigned or further optimized, such parts includes but not limited to impact beam, absorbing parts, longitudinal beam and etc.
For example, the reinforcement of A pillar is BR1500HS thermal forming ultra-high stiffness steel with tensile strength 1500MPa which is able to ensure the safety of the whole passenger cabin
What follows next is the most import part – Restraint system matching and optimization. (Restraint system means the collaboration among front airbag, side airbag, side curtain, safe belt, seats, steering system and pedals)
Through multiple simulation analysis and sled test, R&D team will conclude ECU airbag actuation mode, airbag vent hole size, position and shape etc. to finally choose the most suitable restraint system to match with safety belt, steering column and adopting BOSCH ECU to build a 360 degree protection cabin for the head, neck and chest of passenger cabin.
Built Vehicle Tests
KENBO Built Vehicle Test includes 3 rounds impact tests during Preliminary trial-out, OTS trial-out and Trial production, Sled test, CAE simulation and part improvement are also engaged in each stage. R&D team also constantly improve and optimize spare parts, restraint system and body structure to ensure the final product meets design standard or even higher.
Active Safety
In active safety, KENBO is the best player as it has always been in the market. In the new S7, ESC system, ABS, ASR/TCS/TRC, BAS, HAS and TPMS are available on every model to ensure the safety of every passenger.